Life in the woodworking blogosphere has been a blast for me. I get the opportunity to write about a subject I have a tremendous passion for, and it gives me a chance to tell each of you how excited I am to be building in the shop.
Blogs such as mine, the Wood Whisperer, the Village Carpenter and Matt’s Basement Workshop have an established track record in the blogging community, and while we – and many other established bloggers – like to shine, it’s always exciting to welcome newer members to the community.

Case in point, I’d like you to meet Matt Gradwohl who runs Upper Cut Woodworks out of Washington state. And, as with many other woodworkers, he got his introduction to the craft at an early age watching his grandfather at work “He was a great inspiration. When I was seven or eight years old I built a wooden sled with orange Hot Wheels tracks for the runners. It was a clever idea but weighed a ton and worked horribly. I painted it with tempera paint that didn’t stand up to the wet snow and when I brought it home I was covered in brown paint. It went straight into the fire pit and I swore like a sailor about that “damn sled.” I wasn’t even ten years old but my mom didn’t punish me for the cusswords, she felt so bad for me and was laughing too hard inside.”
Fortunately, Matt wasn’t stopped by his early failure. Later, he converted part of his closet to a computer desk with the help of his grandfather. “I didn’t want anyone to see that I was a computer geek. My grandfather was the first woodworker to teach me proper handsaw technique.”

Today, Matt builds projects in his 25’ x 20’ shop in suburban Seattle. “I bought this house new and when I moved in I had the walls insulated & painted, the floors epoxied, lots of lighting and outlets installed, and a little gas stove installed for heat. I take most of my time off from my real job in the winter, so it’s great to have a warm and well-lit shop to work in.”
With the Pacific northwest such a heavily forested area, Matt loves to use the local timbers in his projects. “I’ve been to a lot of great places in the U.S. and abroad, and I’m always happy to return home. The most common native woods in Washington are Douglas Fir, Hemlock, Western Red Cedar, and Pine.” However, he’s also receptive to using more classic North American hardwoods such as maple, cherry and walnut. “I really like Walnut and especially enjoy the smell of fresh Walnut plane shavings.”
His shop also features a mix of power and hand tools. “I started out with hand tools, then moved to some power hand tools, and then got some big iron. I would call myself and most of the woodworkers I know ‘hybrid woodworkers’ because we use power tools and we’re actively seeking quality hand tools and learning proper hand tool techniques.”
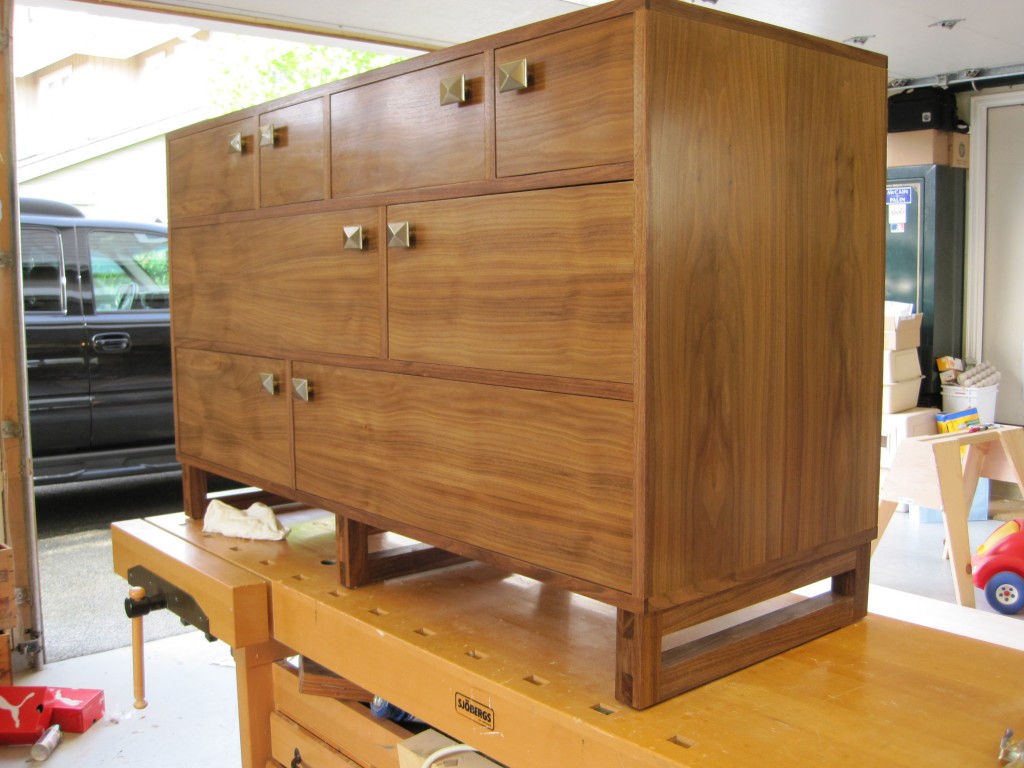
While still working for software giant Microsoft, Matt is working hard to get his woodworking business off the ground. He has moved from building smaller projects into larger and more complicated ones to satisfy the needs of his clients. “Since starting the business earlier this year my first project was the Thomas Walnut Dresser. That was a great project, turned out well, and the client was very happy. I blogged about that project and recently George Walker posted positive comments about it, so that was very cool. The current projects are a custom maple cabinet for a saltwater fish tank, a modern Wenge buffet, and a set of walnut bases for U.S. Fencing Association trophies.”
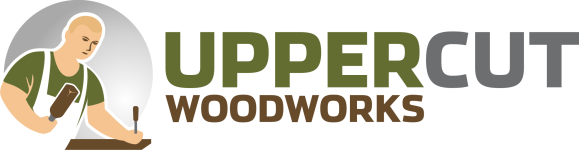
And, part of Matt’s business plan is tied in to his blog. “I decided to get started because I wanted to learn and document the steps for starting a woodworking business. There are lots of blogs that cover design, materials, tools, and techniques and I love all of them. I think it is great that woodworkers help each other so much, I think that’s because we’re dedicated to our craft and we don’t really compete for business. So I am going through the process of starting the business and documenting the steps on the blog. Not only do we need to preserve the designs, materials, tools, and techniques, but we need to get our work into homes and that means creating successful businesses. There’s still so much to do and so much to write about, especially as I head into the end of the first year and the taxman comes knocking, so stay tuned.”
Until then, the blog is hungry, always looking to be fed. “Because I want to produce content for the web on a fairly regular schedule, I need to set aside shop time every week and also set aside time to update the blog. Sunday night has been shop night for me and I often post later that night.”
Matt is quick to point out that Upper Cut Woodworks is a long journey for him – someplace for him to head to after retirement. “In the long term, I’ll be retired from Microsoft woodworking full time, with a good set of design, build, and business skills; a great shop and set of paying customers. Who knows, maybe someday I’ll be writing articles for magazines, teaching woodworking in schools or helping tool manufacturers bring better products to market.”